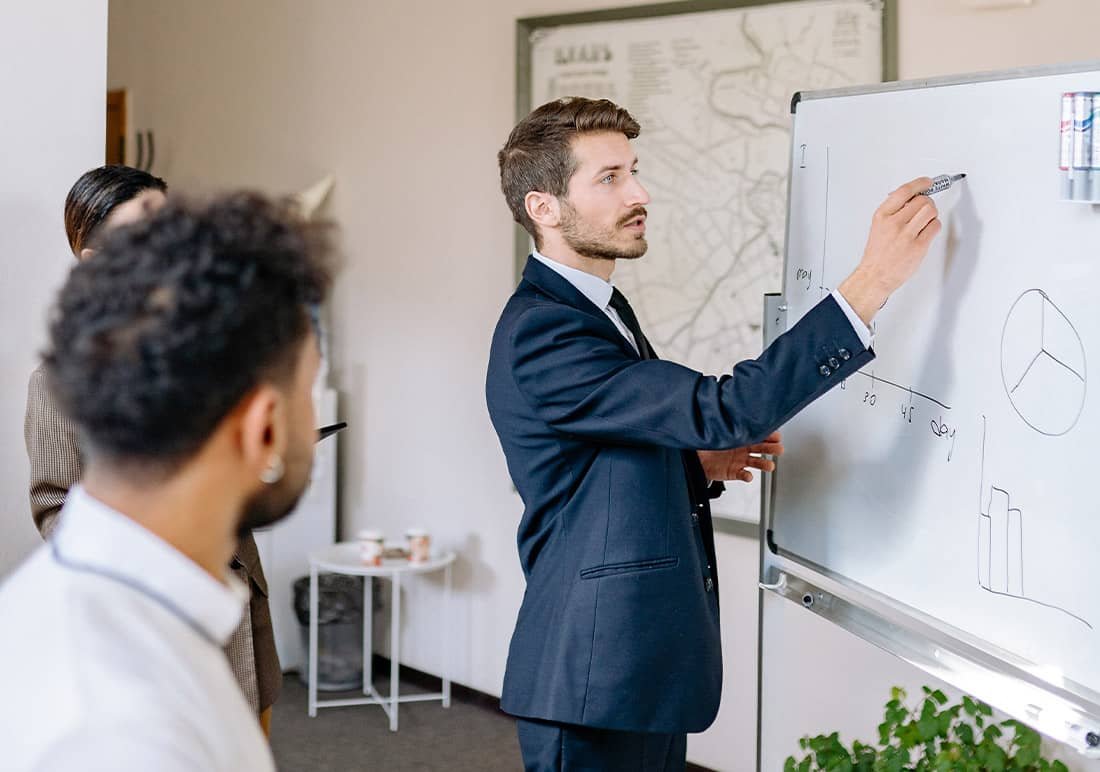
Passionate – Dedicated – Professional
No More Returns
Defect Reduction Success
Achieved a return rate reduction from 15% to 3% within three months by implementing corrective actions, addressing defects such as sagging, uneven support, and fabric tension.
Cost Savings
Improved material sourcing and process adjustments, leading to a significant reduction in return and rework costs while protecting the client’s profitability.
Enhanced Quality Assurance
Increased inspection frequency and targeted training resulted in long-term quality improvements, securing trust from the retailer and strengthening the client’s reputation.
Client Overview
Our client, a leading premium mattress manufacturer, is renowned for producing luxurious, high-quality bedding products. They serve high-end retailers and a discerning customer base. Recently, they faced a challenge when a major retail partner reported an increased return rate, prompting a request for a Corrective Action Plan (CAP) to resolve product quality concerns.
Challenges
The client experienced a 10% return rate on a new mattress line, primarily due to issues like premature sagging, uneven support, and fabric defects. These returns threatened their relationship with the retailer and posed a risk to the brand’s reputation for superior quality. Key challenges included:
Goals
To address the retailer’s concerns and restore product quality, the following goals were established:
How Did It Play Out?
Our team applied a tailored Corrective Action Plan (CAP) for the client’s manufacturing process with the following steps:
The Results
Our six-week corrective action implementation yielded significant improvements for the client:
This strategic approach enabled the client to regain control over their production quality, setting them on a path for long-term success.