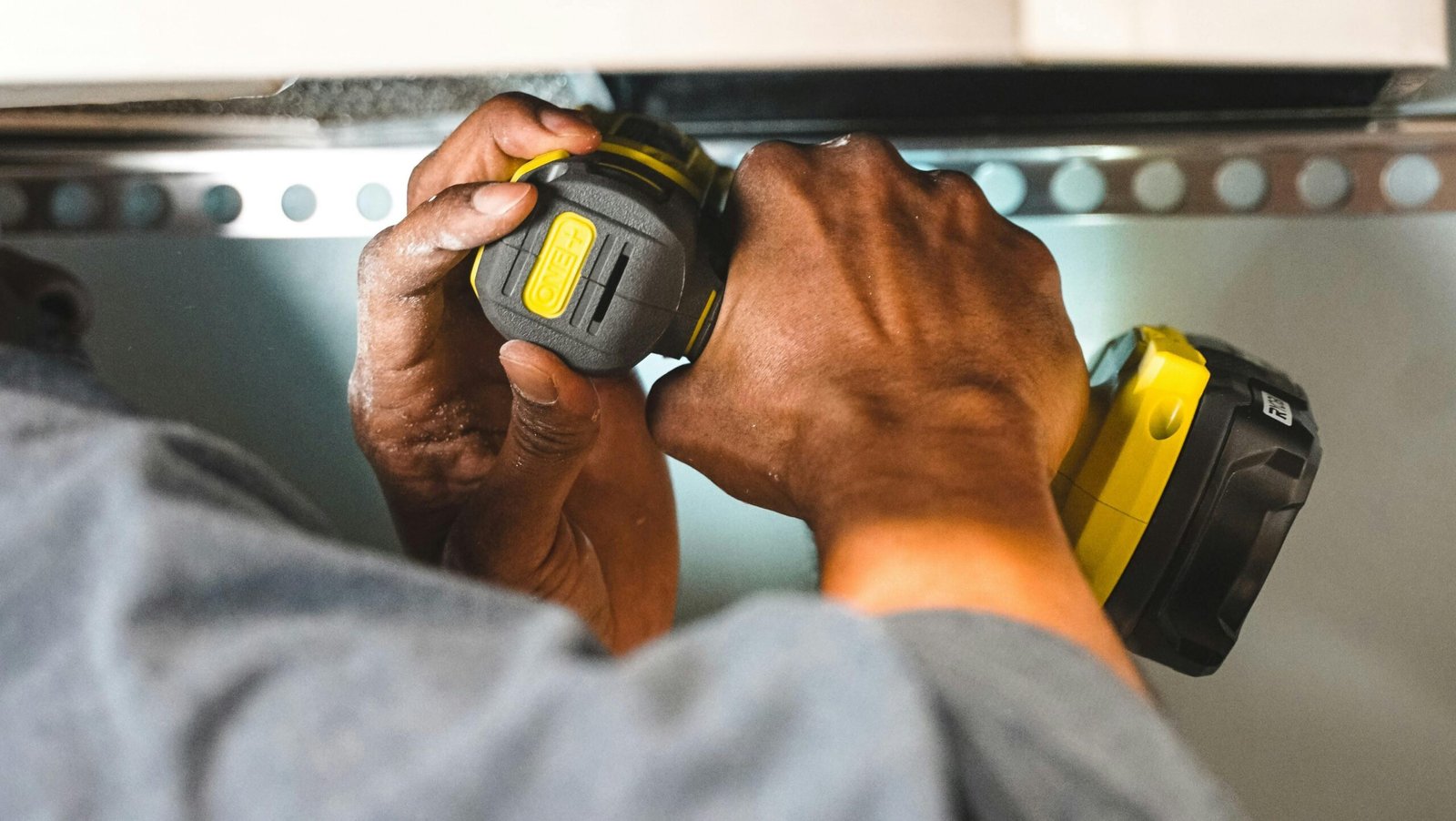
Passionate – Dedicated – Professional
Finished 25,000 tool sets In 7 Days
Restored Product Quality
We replaced 3,200 defective batteries, ensuring all tool sets met the client’s quality standards.
Enhanced Customer Satisfaction
By proactively resolving the issue, we helped the client avoid potential returns and customer complaints.
Compliance Achieved
The disposal and replacement process adhered to industry safety standards, reinforcing the client’s commitment to quality.
Client Overview
A prominent power tools manufacturer approached us when they discovered a significant quality control issue in a shipment of 25,000 tool sets. Known for their durable products, the company wanted to address the problem quickly to avoid impacting their reputation and customer satisfaction.
Challenges
The client faced several urgent issues that could affect both their brand and bottom line:
Goals
To mitigate these risks and maintain their market position, our client outlined key objectives:
How Did It Play Out?
Our team responded rapidly, deploying experts within 48 hours to initiate the inspection and replacement process. Key steps included:
Through a streamlined process, we successfully replaced all defective batteries within seven days, allowing the client to maintain their distribution schedule and restore customer confidence.
The Results
Through our fast and effective approach, the client not only maintained their reputation but also continued to deliver top-quality products, further strengthening their position in the market.