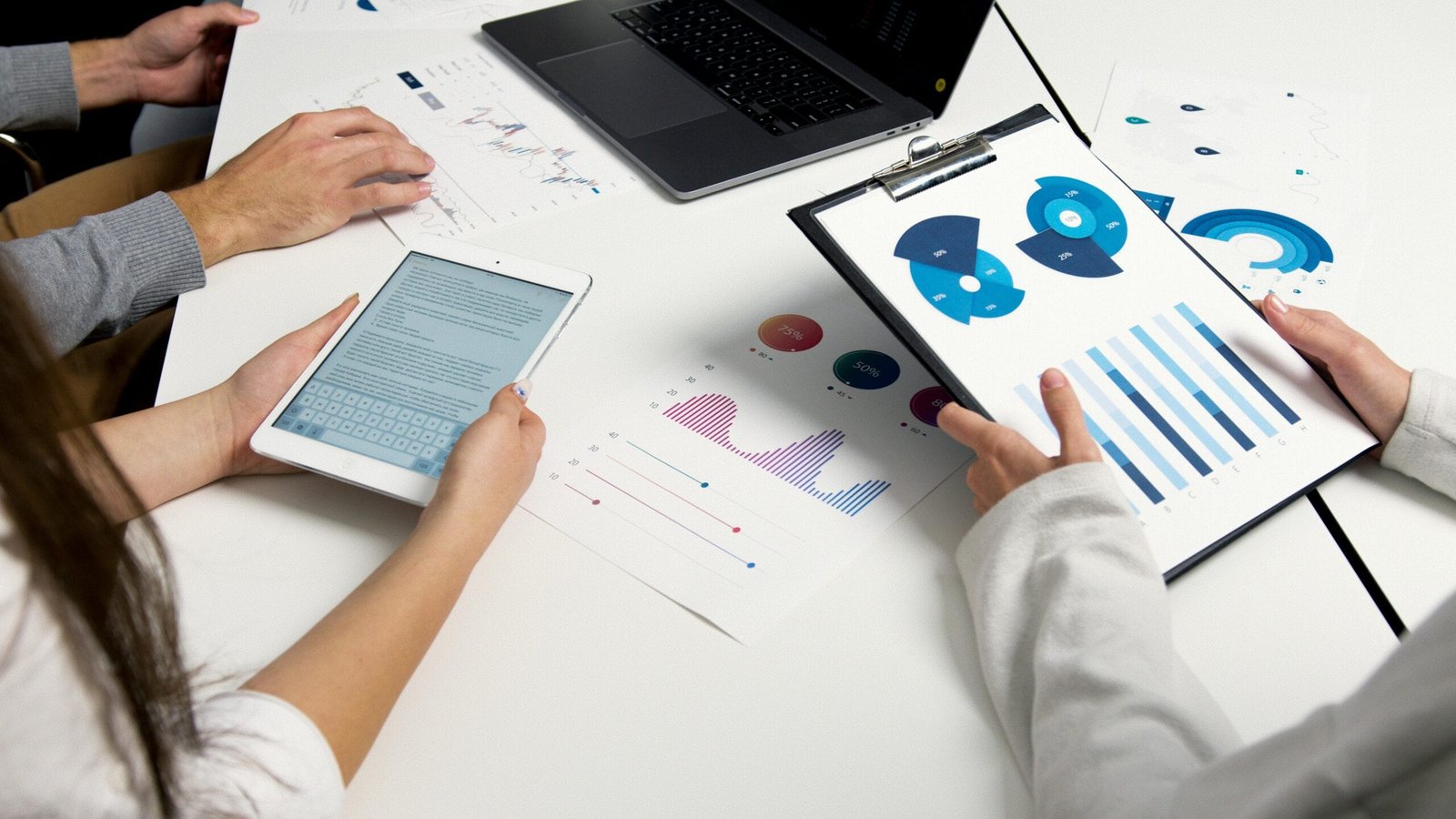
Passionate – Dedicated – Professional
Production Control for Mattress Manufacturing
Defect Reduction Success
Achieved a substantial reduction in defect rates from 13% to 5%, with a target of reaching 3%, ensuring consistent quality across all products.
Cost Savings
Through our Product Control Management System, we minimized rework and return costs, translating into significant cost savings and protecting the client’s profitability.
Enhanced Quality Assurance
Our advanced monitoring and real-time defect tracking provided the client with confidence in their production process, fostering continuous improvement and sustainable quality control.
Client Overview
This client is a renowned North American manufacturer of mattresses and bedding, celebrated for delivering comfort and durability. Despite their success, the company faced an increasing defect rate in their production process, which was impacting customer satisfaction and driving up return rates.
Challenges
The client’s mattress production was experiencing a 13% defect rate, above industry norms. Key issues included:
Goals
To improve product quality and reduce defect rates, our primary objectives were:
How Did It Play Out?
Our team applied the Product Control Management System (PCMS) with the following steps:
The Results
Our eight-week project led to significant improvements for the client:
This strategic approach enabled the client to regain control over their production quality, setting them on a path for long-term success.